SafeLine LYRA discovery slashed lift maintenance expenses by 20%
Lift left in permanent demo mode since installation discovered thanks to SafeLine LYRA – believed to have extended years of the lift lifespan and drastically reducing maintenance costs. "If LYRA had already been installed on the lift when the mistake was made, this would have been detected immediately."
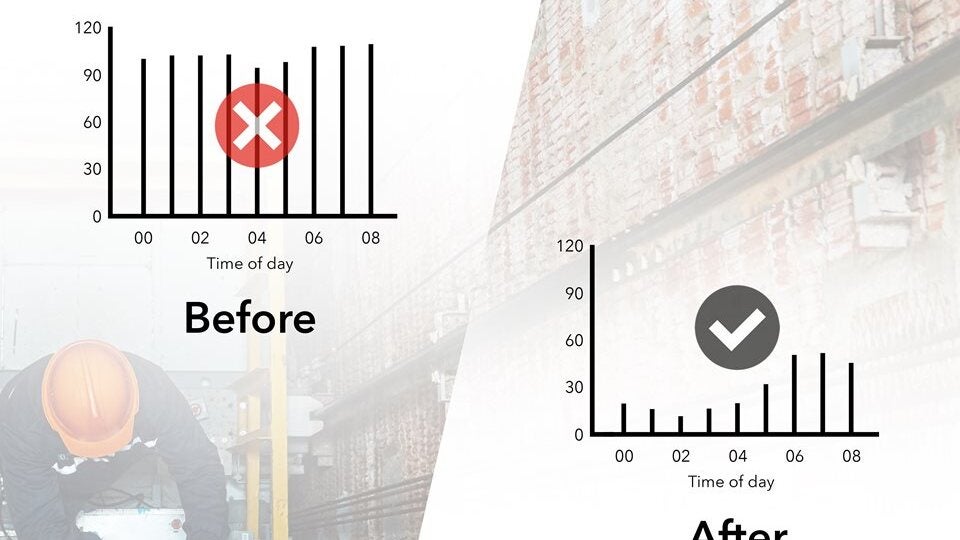
The persistent issues plaguing the lift at the central London shopping centre had become common knowledge among those who worked within the building. Frequent, seemingly purposeless trips up and down the shaft, often occurring at odd hours, had become an unmistakable part of daily life, even though the lift was relatively new.
To pinpoint the root cause of these problems, the maintenance company made the decision to install LYRA, SafeLine's innovative solution, hoping it would shed light on the lift's erratic behaviour. SafeLine LYRA, a compact electronic device, effortlessly integrated into the lift's system, meticulously recorded its journeys along the shaft. This valuable travel data enabled the company to identify irregular movement patterns and make crucial comparisons for diagnostics.
Up to a hundred travels per hour – in the middle of the night
Although the service company was aware of the lift's issues, as evidenced by the unusually high wear on its components and a history of malfunctions dating back to its installation three years ago, they were taken aback by the revelations uncovered by LYRA's analysis of the lift's movement patterns.
"The service company's first reaction was that the LYRA must be broken," says Stuart Garcia.
Stuart is the CEO for SafeLine Group UK and remembers the confused phone call he received from the customer.
“Just a few days after LYRA was installed, they could clearly see that this lift stood out in several ways. The data showed that it was running significantly more often per hour, almost 100 per hour and throughout the night compared to the other similar lifts in the mall, which were at a standstill – something that clearly shouldn't be possible.”
"If LYRA had already been installed on the lift when the mistake was made, this would have been detected immediately"
Upon closer inspection, this turned out to be due to human error. The lift had been put into demo mode by an installer when it was installed three years ago – a demo mode from which it was never taken out of.
“When a lift is in demo mode, the lift is stress tested for a short period after installation to check that everything is working properly. The only problem is that this lift was never taken out of that mode, which meant constant running around the clock for three years. If LYRA had already been installed on the lift when the mistake was made, this would have been detected immediately.”
Comparative product key to unveiling the mistake
A mistake that would have halved the lifetime of the lift and resulted in significant additional costs due to the abnormal wear and tear had it not been remedied in time.
Stuart believes that the failure was not detected by technicians despite several service visits because the fault was simply too simple, yet too large to be detected without the help of a comparative product such as LYRA.
"This time, the problem wasn’t fixing the solution, it was discovering it! If the error had not been corrected in time, the costs could have risen even more, but at least now they could minimise the losses and the lift can be in service for many more years. I would estimate that they have saved at least 20% in total service costs by boosting their maintenance with SafeLine LYRA.”